二甲醚的生产方法浅析
作者/来源:汤洪 日期: 2008-02-20 点击率:4664
1 前言
二甲醚是一种含氧化合物,溶于水、在大气对流层中可降解,是环境友好介质。二甲醚可用于气雾剂、制冷剂、化工原料。二甲醚可做燃料,具有与液化气相类似的性质,而且燃烧完全、热效率高、无黑烟。近年来,由于石油制品的连年涨价,作为洁净环保燃料的二甲醚引起了社会各界的重视。特别是煤基二甲醚生产成本低,与液化石油气有较大差价,使得二甲醚全面替代液化石油气做为民用、工业用燃料成为可能。国内外多家研究机构也正在进行以二甲醚为燃料的汽车发动机研究乃至行车试验。二甲醚做燃料的市场前景十分广阔,同时,生产二甲醚也是当甲醇市场供大于求时甲醇生产企业的一条产业出路。二甲醚的生产方法有合成气一步法、甲醇法两种;而甲醇法又分为甲醇气相催化脱水法和液相催化脱水法。因此,目前二甲醚的生产方法哪种最具工业价值,成为业内人士关注的一个焦点。本文介绍目前国内外可使用的几种二甲醚生产方法,并对这些生产方法的优劣进行各方面的分析比较,为拟投资建设二甲醚生产装置的企业提供决策参考。
2 合成气一步法
以合成气(CO+H2)为原料,合成甲醇反应和甲醇脱水反应在一个反应器中完成,同时伴随CO的变换反应。其反应式为
· 2CO+4H2=2CH3OH
· CO+H2O=CO2+H2
· 2CH3OH=CH3OCH3+H2O
总反应:3CO+3H2=H3COCH3+CO2
典型的合成气一步法生产流程如下:
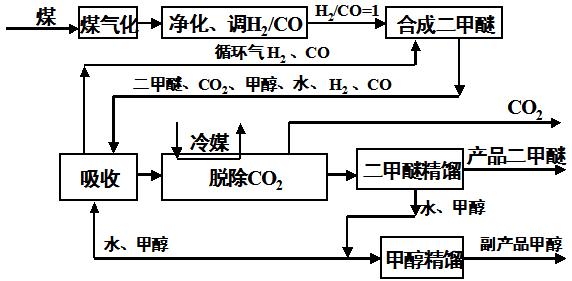
新鲜合成气中的CO和H2的比例配成约1:1左右(配气手段:变换、脱碳等),与循环气混合后进入二甲醚合成反应器进行反应。反应压力2.0~10.0MPa,温度230~280℃。反应产物经冷却、吸收分离,未反应的CO和H2气体返回合成反应器加压循环返回做反应原料。吸收液经脱除二氧化碳、精馏得到产品二甲醚。而反应产物中的甲醇则经精馏提纯后做为副产品。甲醇产量为二甲醚产量的1~10%。
合成气一步法的主要特点在于反应的优势,合成甲醇反应和甲醇脱水反应在一个反应器中完成。反应平衡常数大,合成气单程转化率高,达40,0%~75.0%。国外开发合成气一步法有代表性的公司有:丹麦TopsФe(气相法)、美国APCI(浆态床)和日本NKK公司(浆态床),但都只是作了中试,未见工业化生产的报道。我国的山西煤化所、西南化工研究设计院、大连化物所、清华大学、浙江大学、华东理工大学等也正在进行合成气一步法的研究和探索。
笔者认为,合成气一步法工业化技术尚未成熟。浙江大学研制的一步法合成DME催化剂技术,在湖北田力公司建成了年产1500t/aDME的工业化装置,装置运行不稳定。清华大学在重庆英力建了1套3000t/a的工业试验装置,已生产出二甲醚产品,但由于诸多原因未能连续运行。而曾经炒得沸沸扬扬的、采用美国APCI技术的宁夏宁煤集团830kt/a合成气一步法生产二甲醚的装置,由于生产技术不过关而在可行性研究阶段终止实施。因此,所谓工业化技术尚未成熟,并不是说工艺流程无法实现,而是指关键技术未能有突破性进展,技术经济不过关。而按现有技术生产二甲醚,投资高,生产成本高。实际上,美国APCI和丹麦TopsФe分别在2003年底提出“整体法”和“整体一步法”的概念(即以粗甲醇直接做气相脱水反应的原料,两个反应之间不设甲醇精馏分离装置),并暂时放弃了合成气一步法合成二甲醚的工业化探索。合成气一步法的主要问题有:
1)产品单一,只能生产二甲醚,甲醇产量为二甲醚产量的1~10%,不能调节甲醇和二甲醚两种产品的比例。
2)原料利用率低
在反应产物中二甲醚与CO2的比例为1:1(分子比),如原料中有水或CO2,则反应产物中CO2的浓度(摩尔浓度)将超过二甲醚的浓度(摩尔浓度),而二氧化碳利用价值是很低的。因此,以目标产品二甲醚计,合成气一步法的原料利用率很低,故其生产成本也相应较高。
3CO+3H2=CH3OCH3+CO2
分子量 46.07 44.01
原料利用率 51%
对比甲醇脱水法:
合成甲醇2CO+4H2=2CH3OH原料利用率接近100%
甲醇脱水2CH3OH=H3COCH3+H2O
分子量 46.07 18.015
原料利用率:72.06%
3)合成甲醇、CO变换、甲醇脱水均为放热反应,总反应热效应很大(58.8kcal/molDME),绝热温升达500~1050℃。如不能有效移走热量,则合成甲醇的催化活性中心将被破坏而导致失活。因而必须使用换热式反应器。而无论是固定床还是浆态床,由于反应器效率低,大型化均有一定问题。
4)未找到同时对两个反应均有较好催化作用,且稳定性好的催化剂。这是技术突破的关键。现使用的复合型催化剂两种活性中心相互干扰,甲醇催化活性中心易被氧化而失活,催化剂使用寿命短。
5)分离能耗高:吸收液大量循环,脱除CO2需冷媒,DME粗产品浓度低、精馏分离蒸汽消耗高。
因此,合成气一步法还需要较长时间的研究探索,等待突破性的技术成果完成,其工业化才可能成为现实。
2 甲醇气相法
甲醇气相催化脱水法是目前国内外使用最多的二甲醚工业生产方法。国内拥有该项技术并已工业化的有西南化工研究设计院和四川天一科技股份有限公司、山西煤化所、上海石油科学研究院等。国内技术与国外的丹麦TopsФe、日本NEC、德国联合莱茵褐煤公司的生产方法大同小异。国外主要生产厂家有杜邦公司、阿克苏公司、德国联合莱茵褐煤公司等。典型的甲醇气相法的生产过程如图2所示。
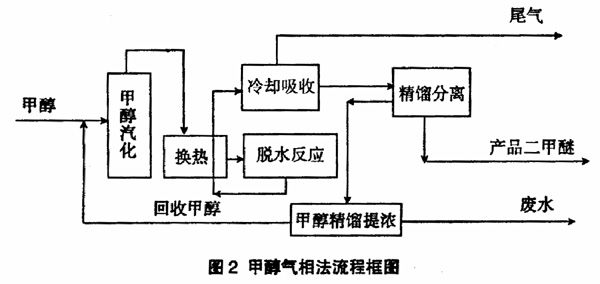
催化剂为ZSM分子筛或γ-Al2O3。甲醇脱水反应的化学反应式为:
2CH3OH=H3COCH3+H2O
主要副反应:
CH3OH=CO+2H2
H3COCH3=CH4+H2+CO
CO+H2O=CO2+H2
反应条件为0.5~1.5MPa、230~400℃。甲醇经汽化在换热器中与反应器出来的反应产物换热后进入反应器中进行气相催化脱水反应,反应产物经换热后、用循环水冷却冷凝。反应器结构有绝热式固定床、换热式固定床、多段冷激式固定床和等温管式固定床等。冷却冷凝后的物料在粗甲醚中间罐进行气液分离。气相为副反应产的不凝气和二甲醚、甲醇的饱和蒸汽,送洗涤塔用甲醇或甲醇—水溶液吸收回收其中二甲醚。吸收液返回粗甲醚中间罐,吸收尾气送出装置。粗甲醚中间罐的粗二甲醚用精馏塔进行精馏分离,从精馏塔顶出来的二甲醚蒸汽经精馏塔冷凝器冷凝后一部分回流入塔,一部分作为产品送产品贮罐。
而从二甲醚精馏塔塔釜得到的甲醇—水溶液则送甲醇提浓塔精馏提浓甲醇,提浓后的甲醇返回做反应原料。从甲醇提浓塔塔釜排出含醇废水。
3 甲醇液相法
液相法由硫酸法发展而来,而硫酸法生产二甲醚工艺是硫酸法生产硫酸二甲酯生产流程中的前半段生产工艺。原生产硫酸二甲酯的企业都拥有液相法技术。山东久泰科技股份有限公司的复合酸液相催化脱水技术在液相法中是国内乃至世界领先的。山东久泰已有30kt/a生产装置,并有多套规模在l00kt/a以上的装置正在规划实施。
液相法反应式仍是甲醇脱水:
2CH3OH=H3COCH3+H2O
反应在液相中进行。目前先进的液相法在硫酸法的基础上有了技术上的突破。如在反应器中加入其他添加物(如磷酸等),改变了反应器蒸发物料的相对组成,从而达到连续反应、反应产物连续蒸发的目的,实现了装置的连续生产、并解决了反应器无机酸催化剂的排放问题。
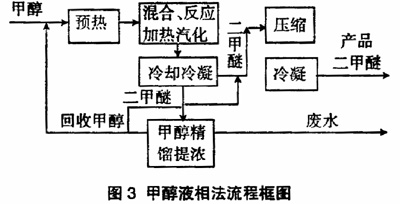
国内先进的甲醇液相法工艺流程如图3所示。催化剂为硫酸等无机酸。甲醇脱水反应在液相、常压或微正压、130~180℃下进行。反应产物加热汽化送出反应器,经冷却,反应产物部分冷凝。汽相经压缩、液化即得到产品二甲醚;反应产物部分冷凝后的液相主要成分为水、甲醇和二甲醚。液相物料经甲醇提浓塔精馏分离,从塔顶得到甲醇和二甲醚的混合物。塔顶冷凝器未冷凝的二甲醚送压缩机压缩作产品,冷凝液则送回反应系统做原料。
液相法的优点在于反应温度低,由于甲醇脱水反应为放热反应,反应温度越低,平衡转化率越高,故其甲醇在反应器中的单程转化率比气相法高,达90%以上。这样循环的甲醇量少,理论上可减少一定的蒸汽消耗。
先进的液相法虽然在原硫酸法的基础上有了多方面的改进,而且逐渐完善,但由于液相法固有的特点,仍存在以下问题:
1)反应在常压下进行;所以需要将产品从常压增压至0.9Mpa以上才能用循环冷却水冷凝液化,压缩电耗太高;反应器物料需混合均匀,不管是用泵强制循环,或用搅拌器搅拌,都要消耗一定的电能。因此,每吨产品的电力消耗在100KWH以上。
2)由于反应温度低,甲醇在反应器中的反应速度慢,甲醇在反应器中需有很长的停留时间,反应器容积很大,例如年产10kt的装置,其反应器直径在4米以上、容积在70m3以上。如大型化需多台并联,故其投资偏高。而且规模越大,比投资越高。
3)由于反应系统有硫酸等强腐蚀无机酸,温度也较高,故其材料为搪玻璃、内衬石墨等,其投资也较高。
4)产品二甲醚与含硫酸等无机酸的反应器物料仅有1块理论板的气液平衡关系,不可避免的含有微量无机酸,影响产品质量。
5)产品二甲醚与甲醇、水的分离也未经精馏,也仅有1块理论板的气液平衡关系,故二甲醚产品的纯度难以提高。若要提高二甲醚产品的纯度,蒸汽消耗还需增加。
6)装置占地大。当装置规模较大时,反应系统多套并联,生产装置占地面积更大。
由此可见,先进的液相法仍有需要改进的地方。如提高反应压力以减少压缩能耗、用精馏方法提纯二甲醚以提高产品质量、强化反应器的搅拌混合以减少反应器的容积,等等。
4 先进的甲醇气相法
西南化工研究设计院是我国最早研究开发二甲醚生产技术的研究单位之一。早在上世纪90年代就已有10来套醇醚燃料和气雾剂级二甲醚生产装置。近年来,西南化工研究设计院和四川天一科技股份有限公司加大了甲醇气相催化脱水法的研究开发力度,开发出完善、先进的独特生产工艺技术。与国内外现有甲醇气相催化脱水法比较,有较大的改进和创新,处国际先进水平。生产过程如图4所示。
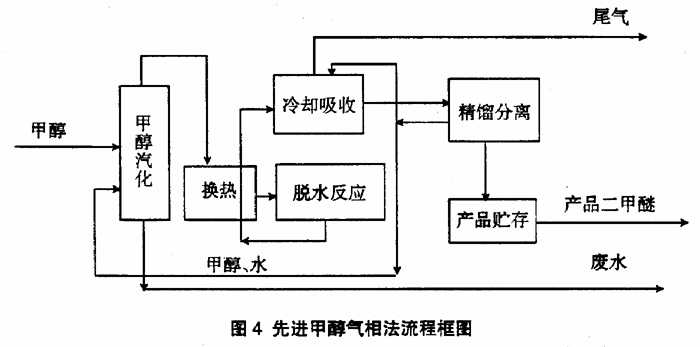
与其他甲醇气相催化脱水法相比,该生产工艺有以下特点:
1)与甲醇装置联产时,可以粗甲醇为原料,可大幅度降低生产成本。
2)反应器采用多段冷激式固定床,催化剂装填容量大,投资低,反应温度适当,副反应少,易于大型化。既避免了绝热式固定床反应器温升太高造成副反应增加、甲醇单程转化率偏低的弱点,又克服了换热式固定床和等温管式固定床反应器尺寸大、催化剂装填容量小的缺点(专利保护关键技术)。
3)采用独特的汽化提馏塔结构和分离工艺,不设置用于回收未反应甲醇的甲醇提浓塔。既简化流程、减少投资,又有效地减少蒸汽消耗。每吨产品二甲醚的蒸汽消耗比国内外同类技术低0.5~1.5吨(专利保护关键技术)。
4)以二甲醚精馏塔塔釜排出的甲醇—水溶液做反应尾气洗涤塔的吸收剂,减少了外排尾气中的甲醇含量,同时由于降低了二甲醚精馏塔进料的甲醇浓度,使得二甲醚分离难度降低,减少回流比,从而节省了蒸汽消耗。
5)采用自行研究开发的专用催化剂,规模生产,活性好、热稳定性好、脱水反应选择性在99%以上。
6)拥有2项中国发明专利。
该技术的主要原辅材料消耗为(以每吨DME产品计):
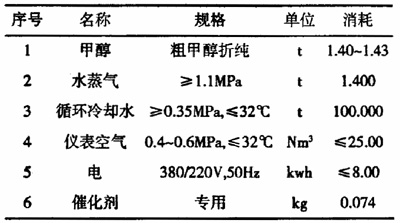
该技术的先进性和实用性已在建在安徽蚌埠和河南罗山的2套万吨级生产装置上得到验证。目前采用该技术的数套生产能力为10kt/a~100kt/a的装置正在建设中。
5 先进的甲醇气相法与先进的液相法的比较
与国内先进的液相法相比较,西南化工研究设计院和四川天一科技股份有限公司的新技术气相法也有一定的优势。其优势主要体现为:
1)投资低,易于大型化。由于反应器与操作工况相似的合成氨厂或甲醇厂的变换炉相比,反应器的直径小、热效应小,易于设计、操作控制和大型化。即使是二甲醚产量为600kt/a的生产装置也只需设置1台反应器,而不需多台并联。
2)电耗低。每吨产品二甲醚消耗的电力比先进液的相法低90KWH以上。与国内先进的液相法的全面比较情况见下表:
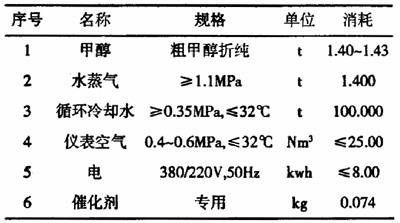
从上表比较的情况看,与先进的液相法相比较,先进的气相法从投资和生产直接成本、稳定操作运行等方面,都有着较为明显的优势。
6 结论
在现有的二甲醚生产方法中,合成气一步法工业化技术尚未成熟,生产成本高,也无工业化装置连续生产的报道;甲醇液相法虽然有技术突破,但仍有投资高、电耗高,生产成本高等问题,而且反应器放大难度大,大装置反应器需多套并联。而先进的气相法投资低、能耗低、产品质量好,而且反应器催化剂装填容量大,易于大型化,是目前最理想的二甲醚生产方法。
