托普索SCR脱硝技术及其催化剂在中国燃煤电厂的应用
作者/来源:崔建华,马楠 日期: 2007-07-18 点击率:4798
1 概 述
随着环境保护的日益严格,对燃煤锅炉烟气脱硝效率的要求已从80%左右到现在许多项目提高到90%,甚至更高。为了设计一套可靠的脱硝系统,使其始终保持理想的脱硝效率并同时保证氨逃逸最小化,在对系统中关键设备进行设计时,要充分考虑系统的实际运行条件,要求把工艺技术、催化剂和工程设计几个方面结合起来。
2 脱硝技术简介
SCR脱硝工艺的反应原理是氨与NOx在催化剂表面上进行催化氧化还原反应,生成无害的氮气和水,反应过程不会生成二次污染物。化学反应方程式如下:

若不用催化剂,上述混合均匀的气体要进行反应,需要900~1100℃温度条件。若采用SCR脱硝工艺,在催化剂存在条件下化学反应发生的典型温度为250~450℃。若使用特殊催化剂,工艺反应温度还可以降至约200℃,也可以高至约550℃。
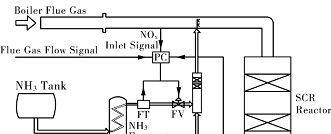
图1 SCR脱硝工艺系统简图
为达到要求的脱硝效率和NH3逃逸量限值,在设计中要充分利用催化剂,尽可能使氨在烟气中分布均匀是非常重要的。反应器入口的烟气分布系统要确保烟气在反应器截面上均匀分布,以确保有效利用催化剂。
催化剂选型必须考虑烟气特点和运行参数范围,但是确保催化剂实现最佳催化效果的先决条件是正确设计关键设备,如:SCR反应器、烟道内部构件和喷氨系统,确保催化剂层烟气流动均匀以及氨和烟气的均质混合,这些都至关重要。通过CFD和实体模型对SCR脱硝装置进行流场模拟是达到这一目的必不可少的手段。
3 托普索公司的脱硝催化剂
SCR脱硝工艺的核心是催化剂,喷入的氨与烟气中的NOx在催化剂表面上反应,生成氮气和水蒸气。通常采用的催化剂是以多孔二氧化钛作为载体,起催化作用的活性成分五氧化二钒和三氧化钨,分布在其表面。我公司脱硝催化剂有不同的型号、不同的通道尺寸(通常叫节距)、壁厚和化学组成,可根据实际运行工况进行选型。节距和壁厚受烟气中灰量的影响,燃煤锅炉脱硝系统一般采用大通道、最小壁厚(0.8mm)的催化剂。
3.1 为防止催化剂中毒设计中需要考虑的因素
在燃煤锅炉高含灰烟气SCR系统中,催化剂会随着活性的损失渐渐老化,主要是因为接触了烟气中的飞灰。催化剂性能退化速率的估计、使用寿命的确定和催化剂的装填设计必须考虑它的运行环境,如:毒物特性、灰尘浓度和潜在的磨损等,归结如下:
飞灰成分对催化剂活性位的化学和物理影响,通常指催化剂中毒;
非常细的飞灰颗粒在催化剂表面沉积,会堵塞进入催化剂活性位的通道或减少其活性表面积;
抑制催化剂孔中的硫酸氢铵冷凝液的产生,否则会减小活性表面积;
催化剂孔的热降解(烧结)会减小催化剂活性表面积;
催化剂通道的堵塞会减少所装载催化剂的有效体积;
若SCR反应器中烟气流动不均匀,飞灰中的颗粒会造成催化剂磨损。
如果脱硝系统设计不合理,任何类型的催化剂,如:板式、挤压蜂窝式或波纹蜂窝式,都可能被磨损。见图2。
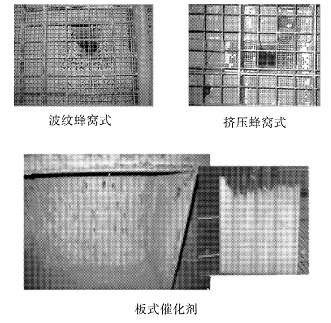
图2 不同形状的催化剂磨损示意
SCR脱硝系统催化剂选型设计需要考虑以下因素:
要求的脱硝效率;
反应器出口烟气中未反应氨气(氨逃逸)的最大容许量;
为避免后续设备不受硫酸铵影响,系统可接受的最大SO2/SO3氧化率;
催化剂理想寿命和基于烟气中灰量和其他成分得出的催化剂预期失活速率。
很显然,只有全面了解这些因素对催化剂性能的影响,才能选出最适合的催化剂类型。合理设计催化剂工艺,才能保证催化剂的最佳性能和最长的寿命。
3.2 托普索公司催化剂的特点
托普索公司创立于1940年,自行开发了各种催化剂和工艺技术。公司在不断发展的基础上,还进行了大量的研发工作,为各种工况条件提供最适合的催化剂。托普索公司拥有各种类型的催化剂制造技术,但在电厂烟气脱硝系统中主要采用脱硝专用波纹蜂窝催化剂,该催化剂集板式和挤压蜂窝式催化剂的优点于一体,对防止各种原因导致的催化剂中毒具有很好的抵抗能力。其优点概括如下。
(1)由于托普索公司催化剂独特的制造工艺,催化剂基板采用加固玻璃纤维,比金属板式催化剂或挤压蜂窝式催化剂重量要轻许多。由于重量轻,其运输、吊装都很方便,且对于SCR反应器钢结构和地基的荷载比较小。
(2)由于托普索脱硝催化剂的孔型为不规则形状,是独特的波纹状,所以其比表面积很大,且孔隙大小分布呈多样性。大、中、小孔隙按一定比例分布。试验研究和实际运行经验均证明该催化剂结构对增加表面活性位、减少表面SO2氧化活性位是非常有利的,如图3。
(3)根据显微镜观察显示,托普索催化剂具有三种大小不等的孔隙结构,分别为100Å、1000~2000 Å和50000 Å,见图3。通过各种类型的催化剂进行观察,发现砷气多聚集在微孔内。所以与其他类型催化剂相比,托普索公司独特的孔隙结构能大大减少砷气聚集,从而减缓对催化剂的毒害。
(4)由于具有柔韧的纤维结构,这种催化剂可以在高温下运行,具有非常好的抗热应力能力。催化剂的边缘经过加固,可以抵御含尘烟气的磨蚀。催化剂运行温度在220~450℃范围,可抵御800~900℃的高温环境。催化剂可承受的最大温升可达150℃/min,这是其他类型催化剂无法相比的。
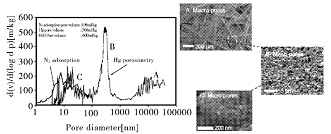
图3 托普索脱硝催化剂三种孔径分布
4 流场模拟的作用
SCR反应器、烟气通道、喷氨和混合系统的合理设计,是催化剂实现最佳性能的必要前提。在高尘脱硝装置中,必须采取措施确保催化剂层的理想烟气条件,以避免出现上述类型的催化剂堵塞或磨损,减少损失。
运用CFD或实体模型进行烟气流场模拟已被证实是达到上述设计的有效且必要的措施。模型工作通常的目的是:
确保喷氨之前烟气流速高度均匀
验证烟气与氨的混合效果
在给定的约束条件下优化烟道和反应器的布置
开发并优化必要的流量控制装置
确保第一层催化剂入口处烟气速度高度均匀
确保烟气流动与垂直方向的夹角最小
确保不增加沉积灰量
使系统压降最低
尽管使用功能强大的计算机进行流体力学模拟更快捷有效,但对飞灰的运动(如:沉积和二次夹带)进行模拟的理论基础仍很薄弱,而且导流板的优化经常需要反复进行。所以对于高尘脱硝系统设计,要实现预防灰沉降和磨损这些主要目标,通常采用实体模型方法,实践表明该法行之有效。
5 托普索公司催化剂工业应用情况
托普索DNX催化剂广泛用于世界上不同煤种的项目中,拥有381个项目业绩。所有项目的实际运行情况均证明催化剂中砷的聚积对托普索催化剂的性能影响并不明显。实验室研究表明,吸附气相中超过1%(重量)的砷,催化剂活性只降低10%。对一些使用DNX催化剂的高尘SCR装置中砷聚积和失活速率的监测表明,DNX催化剂具有抵抗砷中毒这一特性。
5.1 阳城电厂二期工程烟气脱硝项目
山西阳城电厂二期工程 8号600MW机组燃用的无烟煤来自山西阳城当地煤矿。按进度要求,SCR脱硝装置在2007年初启动运行。托普索公司为该项目提供催化剂和脱硝系统设计,以及为验证设计所需进行的实体模型模拟。基本设计数据如下:
600 MW
烟气流量2300000 m3/h
两层DNX催化剂
NOx含量1300 mg/m3
含灰量<20 g/ m3
脱硝效率80%
氨逃逸<3×10-6
SO2 氧化率<1.0 %
5.2 国华台山热电厂
台山电厂目前有5×600MW燃煤机组,托普索公司为其5号机组设计了SCR脱硝系统。托普索公司为其脱硝系统提供催化剂、系统关键设备和系统设计,包括实体模型试验。基本设计数据如下:
600 MW
烟气流量1900000 m3/h
两层DNX催化剂
NOx含量550 mg/m3
灰量 14 g/ m3
高达94% 的脱硝率
氨逃逸<3×10-6
SO2 氧化率<0.75%
该项目已投运,在选用催化剂时特别考虑了灰中高钙成分(CaO 28.9%)的影响,美国PRB煤项目中遇到过类似的高含钙量情况。氧化钙会与烟气中SO3反应生成石膏CaSO4而覆盖在催化剂表面,由于托普索脱硝催化剂具有三种孔径分布,具有非常高的抵抗“中毒”能力,包括由灰中高含量钙所引起的“中毒”,即使表面有大量的石膏覆盖,还会有到达活性位的可用通道。
该系统设计保证脱硝效率为94%,氨逃逸率只有3×10-6,实现这一设计需要催化剂具有高性能且对氨/NOx混合的要求更高。当要求高脱硝效率和低氨逃逸率时,系统设计要素达到适宜平衡是非常关键的。对脱硝效率和氨逃逸量的要求越严格,对氨和烟气(NOx)混合的要求越高。
托普索公司开发了专有混合装置——星形混合器(图4),由一些形状为带四角星的圆盘组成。星形混合器按照一定的角度安装在烟气通道中,使盘后气流形成涡流。该装置实现了短距离内最佳的混合,且压损很小。
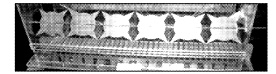
图4 托普索公司专有星形混合系统
台山项目5号机的脱硝系统通过安装星形混合器,并结合流场模拟,可以使系统在达到94%脱硝效率、3×10-6氨逃逸量所需的理想混合效果的同时,系统压损小于339 Pa(不包括催化剂层压降)。
6 结 论
NOx排放法规的要求越来越严格,为了在燃煤锅炉高灰分情况下,实现SCR脱硝装置的高脱硝效率并保持最小的氨逃逸量,认真选择催化剂类型和正确设计系统是至关重要的。
托普索公司脱硝催化剂是经过实际运行验证具有非常好的抗中毒性能的催化剂。系统设计充分考虑了各种因素的影响,如:煤的高灰分、灰中含钙、碱金属等。系统还配备有效的催化剂清灰系统。在验证高尘SCR系统设计合理性时,还应用烟气流场模拟方法。流场模拟有两种方式,一种是CFD模拟,另一种是实体模型模拟。在设计阶段应用实体模型模拟可以验证烟气流速分布均匀性,确定烟气流动调节装置的布置,评估飞灰的沉积和分布状况。
托普索公司独有的催化剂性能和扎实的工程设计能力,必定会为中国烟气脱硝净化领域提供最好的技术和服务。
