氮肥(甲醇)厂联产二甲醚循环经济项目
作者/来源:杨奇申 (河南省石油和化学工业协会 郑州 450003) 日期: 2007-03-01 点击率:5864
0 氮肥厂联产DME提纲
(1)用YQS技术把氮肥(甲醇)厂变成绿色煤化工基地符合循环经济的要求;
(2)YQS发明专利及独特的技术路线;
(3)独创成熟自主知识产权的专用催化剂;
(4)6家应用实例与企业联盟十、百、千万吨的二甲醚生产及产业化发展计划;
(5)组建企业联盟的技、研、产、销、培训、互联网信息服务一体化产业体系;
(6)以公路河流DME供给线与城市DME供应网络相结合的全国二甲醚营销体系;
(7)配套的产业政策和资金投入是二甲醚产业快速发展替代石油燃料的前提条件。
1 用YQS技术把氮肥(甲醇)厂变成绿色煤化工基地符合循环经济的要求
1.1 把氮肥厂办成绿色环保型企业
YQS10066二甲醚生产技术是基于我国氮肥企业的技术改造而创新设计的“间接一步法”联产DME发明专利技术,充分利用氮肥生产过程中部分未反应的合成气变成DME的生产原料气,DME生产过程中排出的的气态和液态废气废料均被回收利用,冷却循环水进入闭路循环系统循环利用,每万吨DME需要冷却补充水200 t,达到国家要求的排放标准,并利用循环经济理念,实现绿色环保型可持续发展企业。
1.2 变废为宝生产出高利润的DME
给氮肥企业带来新的利润增长点。因为DME的批发价格为4200~4500元/t,利润为1200元/t。而1t化肥的利润在100~400元之间。氮肥厂可在不影响氮肥的产量不增加能耗的情况下按30%设计,考虑到化肥的淡季减少氮肥的产量增加DME的产量按50%设计。以年产300 kt合成氨为例,可联产DME100~150kt,年营业额增加4.3~6.45亿元,年利润1.2~1.8亿元。
全国每增加10000 kt DME,氮肥企业就增加450亿元的营业额,利润120亿元左右,将有力的支持三农建设,并可以调节化肥的供求平衡。
1.3 投资少、周期短、见效快
10000 kt DME效益分析:
投资少:改建1家相同吨位的氮肥厂的投资,仅相当于新建1家DME工厂投资额的十分之一。无联醇装置每万吨平均投资550万元,首个10 kt投资800万元,每增加10 kt增加投资500万元。有联醇装置(甲醇厂)每万吨投资300万元。
建设周期短:YQS技术充分利用氮肥厂的大部分设备和公用设施,仅增加脱碳、脱硫、甲醇和DME合成、精馏设备,减少了新建DME工厂的基建、公用设施、造气工段的建设。有联醇装置(甲醇厂)建设周期3个月,无联醇装置建设周期6个月。
见效快:3~6个月建成投产,4~7个月就开始销售,资金回笼快,当年投资当年收回成本并盈利。
1.4 50000kt的生产潜能延长了氮肥企业的产品链和价值链,提高了资源利用率
氮肥企业可联产20000kt:我国500多家氮肥企业,2005年全国年产合成氨45962.5kt,氮肥35759.1 kt,尿素19948.8kt,在不影响3种产品产量又不增加能耗的情况下,按产能的50%设计可联产DNE20000kt,考虑到淡旺季产能的波动,也可按60%设计DME的产能为25000kt。
甲醇过剩可迅速扩大DME的产能8000~15000kt:2005年底精甲醇的产能为5356.4kt,2006年底将接近20000kt,2007年底将达到30000kt,而甲醇的下游市场并没有完全形成,甲醇的过剩是必然的。利用YQS技术把过剩的甲醇生产成DME。按1.5t的粗醇可生产1tDME,3个月即可投产。
还可发展DME的下游产品烯烃。把遍布全国的氮肥企业办成绿色环保型的煤化工基地网络,便于就近销售,运距短(50~500km)销售费用低,利润高。
2 YQS发明专利及独特的技术路线
独特的技术路线:在利用大部分合成氨设备的同时,充分利用甲醇的反应热进行二甲醚的脱水反应,又利用二甲醚的反应热进行精馏,既解决了“两步法”的高耗能问题,又避免了“一步法”的变换反应,实现了二甲醚生产的低耗,节能,零排放,高附加值。满足了区域循环经济发展的要求。
独特的设计理念:YQS发明专利是杨奇申高工与研究人员历经10年研制成功的二甲醚生产技术,已获国家发明专利(专利号:ZL01106607.5),属于间接一步法,清华大学倪维斗教授称之为“双塔一步法”。设计理念是经过甲醇合成塔合成的粗甲醇热气体直接进入二甲醚合成塔,通过分离和精馏既制取DME,不需要先制取甲醇,节省了设备降低了能耗。
2.1 YQS醇醚合成工艺(见图1)
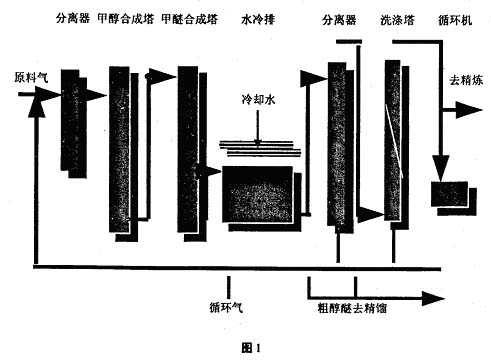
原料气经油水分离器后进入甲醇合成塔,在一定温度、压力及催化剂作用下,合成为粗甲醇,粗甲醇热气体和氢、氮气混合物直接进入醚合成塔,在一定温度、压力及催化剂作用下,甲醇脱水生成二甲醚,醇醚混合物经冷却后送入醇醚分离器,分离后的气体经洗涤送精炼工段(或甲烷化工段即:构成甲醇、甲醚、甲烷化三甲工艺),而分离出的醇醚混合物送入中间储槽,后送加压串低压精馏工段,生产出99.9%高纯度二甲醚或配制成醇醚民用燃料替代石油液化气出售。
2.2 YQS醇醚精馏工艺(见图2)
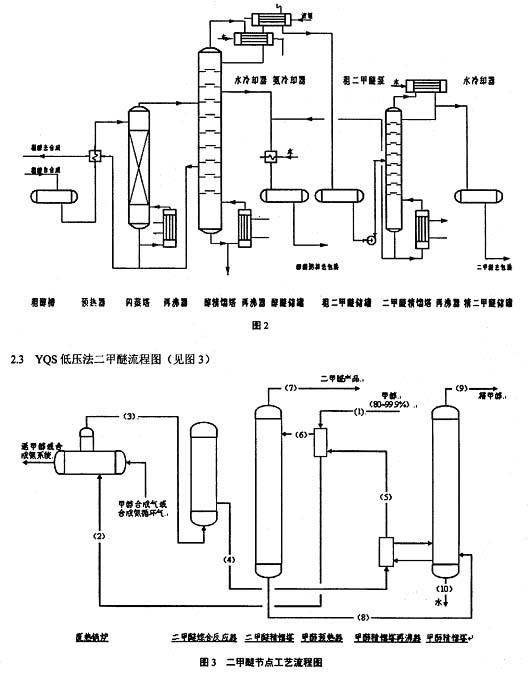
2.4 YQS4醇醚合成工艺的3种应用形态
(1)高压法醇醚合成工艺:压力125~130Mpa;
(2)中压法醇醚合成工艺:压力53~60MPa;
(3)低压法醇醚合成工艺:压力6~10MPa;
(4)后两项也已申报国家发明专利。
3 独创成熟拥有自主知识产权的专用催化剂
独创成熟的专用催化剂是与山西省煤化工研究所联合研制成功,并拥有自主知识产权,有6大特点:
(1)DME选择性最高的优良催化剂;
(2)转化率高:75%~80%;
(3)寿命长:2年;
(4)温度低:280~320℃;
(5)低浓度转化:高空速粗甲醇热气体中甲醇纯度较低时可保证其转化率;
(6)成本低每吨低于9万元。
“双塔一步法”催化剂小试实测数见表1。
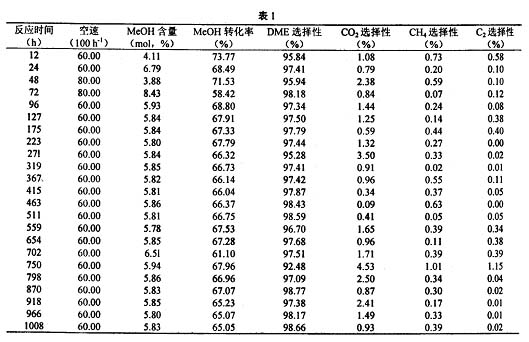
4 应用实例与十、百、千万吨产业发展计划
贵州全省1000kt,毕节100kt,无联醇装置首建20kt,2006年10月投产,贵建投与毕节化工公司联合投资。
河南息县化工总厂100kt联醇首建20kt,2006年8月投产。
河北邱县龙港联醇50kt,首建10kt,2005年2月投产,2006年5再扩产10kt,2006年7月正常运转批量生产。
河南博爱源泰化电联醇100kt,首建20kt,2006年10月投产。
湖南衡阳化肥厂无联醇30kt,在建2006年12月投产。
首期在建130kt,年内扩建至450kt,累计1350kt。
现与兖矿、晋煤、兰花、建滔旭阳、山西光大焦化等30多家意向5000kt。
4.1 YQS专利技术的产能设计
(1)已实施单产设计生产能力:年产10kt、20kt。
(2)YQS技术设计能力:年产50kt、100kt、200kt。已为多家企业作可研报告并立项。
(3)YQS技术最大设计能力:单塔合成300kt。多塔并联可实现年产1000kt以上的生产能力。
(4)百万吨DME产能的设计:采取四塔并联即1台100kt合成塔,3台300kt的合成塔。或200 kt和300kt的合成塔各2台四塔并联。可联产可新建。
(5)能源基地新建DME生产基地的设计:年产200kt投资10亿元,建设周期18~24个月。
4.2 十、百、千万吨DME产业化发展计划
(1)十万吨系列示范项目在2006年底前全部投产运行:河北龙港、河南息县、博爱、贵州毕节各 20kt小计80kt,湖南、山西、河南小计50kt,共130kt,总结经验再推广。
(2)重点地区百万吨DME重点项目建设:2006年底前全部开工,以山西兰花和晋煤集团、绿洲公司,山东兖矿集团、金能公司,陕西绿源公司、贵州毕节等10多家公司共同实施百万吨重点建设计划。在2007年6月底前投产运行。探索以公路沿线和城市DME加气站网络相结合的营销模式。
(3)千万吨DME产业化建设工程:以改造大甲醇厂和大化肥为主,调动上市公司和投资公司的资金,快投入快产出。争取国家专项资金的扶持。从2006年6月至2007年12月底前全部实施,2007年12月实现8000~10000kt的生产规模。替代进口LPG为国家节省外汇37~46.3亿美金。
4.3 十、百、千万吨DME产业化发展的意义
(1)是进一步检验YQS技术在不同规模条件下的应用情况,总结经验,以利于在更广的范围内推广应用。
(2)是只有形成10000kt的产能才能形成中国DME完整的产业链,使DME从技术研发、生产、储运、销售、到应用技术推广的每个环节,形成完整良性循环的产业链条。
(3)是探索出一条适合中国的DME新能源发展之路,既不能过剩也不能短缺,循序渐进的稳步发展。
(4)是为综合利用煤制气、焦炉煤气、煤层气提供科学的依据,在节约能源,不增加能源消耗的情况下,把生产化肥的废气、焦化炼钢的焦炉煤气、煤层气(瓦斯)变废为宝,生产新的能源DME。
5 DME的技、研、产、销体系
(1)组建企业联盟共同完成了YQS的技术研究和全系统的服务体系建设。
(2)与山西煤化所联合开发并生产催化剂,已供应市场。
(3)与河南天一公司、石家庄正元公司、新乡金鑫公司共同开发DME生产的专用设备,已投放市场。
(4)与郑州大学、河南化工设计院、安淳公司联合进行项目可研、工程设计、等工作。
(5)北京思创公司提供专用DCS自动控制系统。
(6)健康中国网二甲醚频道(京ICP证040585号):提供互联网远程咨询培训和监控系统,可为客户提供一条龙的交钥匙服务工程。
(7)与安阳贞元集团联合以LPG专列和汽车槽车提供储运服务。
